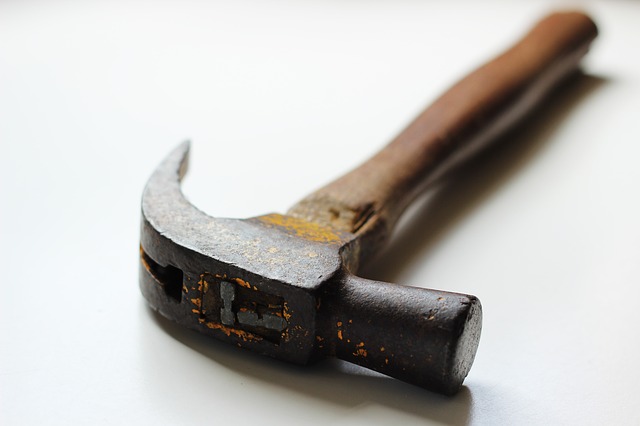
Vi har alla någon gång hört talesättet ”Om det enda verktyg man har är en hammare tenderar man att se varje problem som en spik.” Den gyllene hammaren skrevs först av Abraham Kaplan 1964: ”I call it the law of the instrument and it may be formulated as follows: Give a small boy a hammer, and he will find that everything he encounters needs pounding.” Men den mer populära varianten kommer från Abraham Maslows The Psychology of Science, från 1966.
Utgår vi från att Lean production är ett verktyg, vilket många felaktigt gör, skapat för bilindustrin och försöker applicera det på andra verksamheter skapar man troligtvis mer problem än vad man tidigare haft, eller så uppnår man nollresultat eftersom nya problem uppstår medan andra försvinner.
Lean production är en filosofi om hur man arbetar med att identifierar och eliminerar slöserier för att maximera den värdeskapande tiden man arbetar med produkter eller tjänster.
Många framhåller Toyota Production System (TPS), vilket för övrigt byggdes upp innan Lean fanns som en definition, som ett föredöme. Och i TPS finns verktyg som 5S, Just-in-Time, 7+1 slöserier och många fler. Problemet är att många okritiskt försöker kopiera TPS utan att förstå vad som gjort Toyota, åtminstone historiskt sett, till ett framgångsrikt företag.
Man kan, och till viss del bör, kopiera dom verktyg som Toyota Production System innehåller. Men samtidigt är inte alla verktyg applicerbara inom alla organisationer, eller på samma vis som vid Toyotas produktion av bilar. Dessutom bör man själva utveckla sitt eget produktionssystem, med egna verktyg, egna värderingar och principer.
Som du förstår blir det problem om man med Toyotas produktionssystem i bakhuvudet försöker att implementera Lean production i exempelvis en skolmiljö, eller inom tjänstesektorn. Detta betyder givetvis inte att man bör undvika Lean på sådana arbetsplatser, utan att man bör fundera på vad man vill uppnå, varför man vill uppnå det och hur målet skall uppnås.
Tidigare har jag skrivit om Paul A. Akers, entreprenör, grundare och ägare av FastCap LLC., ett företag som tillverkar ett flertal olika produkter med inriktning mot hantverkare. I sin bok 2 second lean beskriver han hur företagets egna verktyg fungerat mycket bättre för dom, än exempelvis Kaizen event. Och av videoklippen på YouTube att döma så ligger företaget i framkant vad det gäller medarbetardriven utveckling av arbetsmetoderna. Trots att det ofta är mycket små förändringar som kontrolleras med tidtagarur och dokumenteras med en mobiltelefon.
Så, för att avrunda. Vad har jag tagit upp i detta blogginlägg? Att Lean production inte är en hammare och att alla organisationer är olika och inte bör behandlas som spikar. Du har också kunnat läsa om att även om det finns framtagna verktyg behöver inte det betyda att dom nödvändigtvis är rätt för din arbetsplats, det kanske behöver utvecklas skräddasydda verktyg just för era arbetsuppgifter.
Till sist. Förbättringsarbete skall vara kul, annars händer det ingenting!