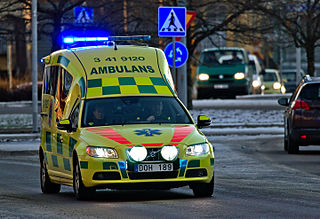
Min upplevelse av den svenska sjukvården är att den är byggd som en klassisk stuprörsorganisation där landstingspolitikerna fattar beslut som sedan, efter bästa förmåga, skall genomdrivas av sjukhusledningen, och längst ned står undersköterskorna och sedan vi, du och jag, våra föräldrar och eventuella barn. Vi kan uppleva den svenska sjukvården som en aning trög, sjuk- och undersköterskorna upplever att dom har väldigt mycket att göra, men får lite tid och sjukvården brottas med dålig ekonomi och hög beläggning.
På sociala medier läste jag Anna Strands tweet om att lean skulle vara Neo-Taylorism, och fortsatte att läsa utläggningen i blogginlägget Hur kunde det bli så lean and mean? där man får följa hennes upplevelser i hur den svenska sjukvården säger sig ha implementerat lean i sin vardag. Men ingenting av det jag läser framstår för mig som lean. För mig låter det mer som att sjukhusledningen, av några överbetalda managementkonsulter, försökt implementera någon form av rationaliseringsstrategi som man missuppfattat, antagligen på grund av ojuste marknadsföring, som lean.
Spagettidiagram, frekvensanalyser och tidsstudier kan vara effektiva, men bör i första hand inte användas för att få anställda, i detta fallet, på sjukhusen att springa fortare, utan för att upptäcka rörelsemönster, flaskhalsar för att kunna minska slöserier och icke värdeskapande arbete vilket kommer ge mer tid för patienterna.
Ett intressant exempel är William Stridsberg och David Örneblad examensarbete ”Flödesanalys samt frekvensstudie vid Alingsås lasaretts akutmottagning” som fick Lean Forums pris i kategorin bästa examensarbete 2015. I dom båda länkarna finns dels en sammanfattning, men också en länk till examensarbetet som utfördes på Alingsås lasaretts akutmottagning.
Som Niklas Modig och Pär Åhlström skriver i Detta är lean så är det inte säkert att dom verktyg och metoder som är en del av Toyota Production System inte alltid applicerbara i andra organisationer och om man försöker att kopiera och införa andra företags produktionssystem på en väldig låg abstraktionsnivå risker man att förlora hela filosofin, och bakgrunden, till varför det fungerar just för det företaget. Ett sjukhus är ingen bilfabrik och kommer aldrig att fungera som en heller.
Personalen flyr som man gjorde redan vid Fords löpande band. För ingen vill ställa upp på att tvingas på en människosyn så diametralt olik den jag har. Varför inte se sanningen i vitögat. De där leankosnulterna som tvingande mellanchefer att bygga med lego och anställda att klistra post it lappar på stora tavlor borde ställas till svars för den människosyn de representerar.
Citatet ovan är troligtvis en normal syn, inte bara inom sjukvården, i alla organisationer där man försöker implementera något som på pappret låter som lean, men i praktiken blir något helt annat. Citatet vittnar om att konsulterna dels inte förstår organisationen samt inte lyckats kommunicera varför man bör tänka på sjukvården ur ett flödesperspektiv.
Jag har aldrig arbetat inom landstingssjukvården och har, tack och lov, endast haft sporadisk kontakt med traditionella sjukhus som patient. Men inom alla organisationer finns det utmaningar. Det kan handla om att förråden ser ut som en krigszon och är överbelamrade med lager som är dåligt uppmärkt och står huller om buller. Ett annat problem kan vara brist på just sjukvårdsartiklar, att man alltid tvingas hämta dom redskap som krävs för en undersökning, istället för att dom är placerade och rutinmässigt påfyllda i varje undersökningsrum. En fungerande lean-organisation bygger på medarbetarnas engagemang och ledarnas förtroende för detta, inte på en pressad lednings vinande piska.
Arbetar du inom sjukvården, har du erfarenhet av hur det fungerar, vad som inte fungerar så skriv gärna en kommentar. Vad stör du dig mest på under arbetsdagen? Krångliga IT-system, hanteringen av mat till patienter eller att det kanske saknas katetrar och kanyler?